How to convince a customer: test your product a million times
Tunnel dampers must be custom-made to the millimeter to fit any layout. Brutal testing in 400–1000 degrees Celsius ensures reliable operation. When it comes to budget, transportation cost of heavy-duty tunnel dampers can be a surprise – pleasant or unpleasant!
Ensuring fire safety is imperative in designing large tunnels. The reasons are obvious. In an underground space, the spreading of heat, smoke, and toxic gases can be catastrophic if proper precautions are not planned. Tunnel dampers are among the most essential fire safety equipment. No large tunnel is built without them.
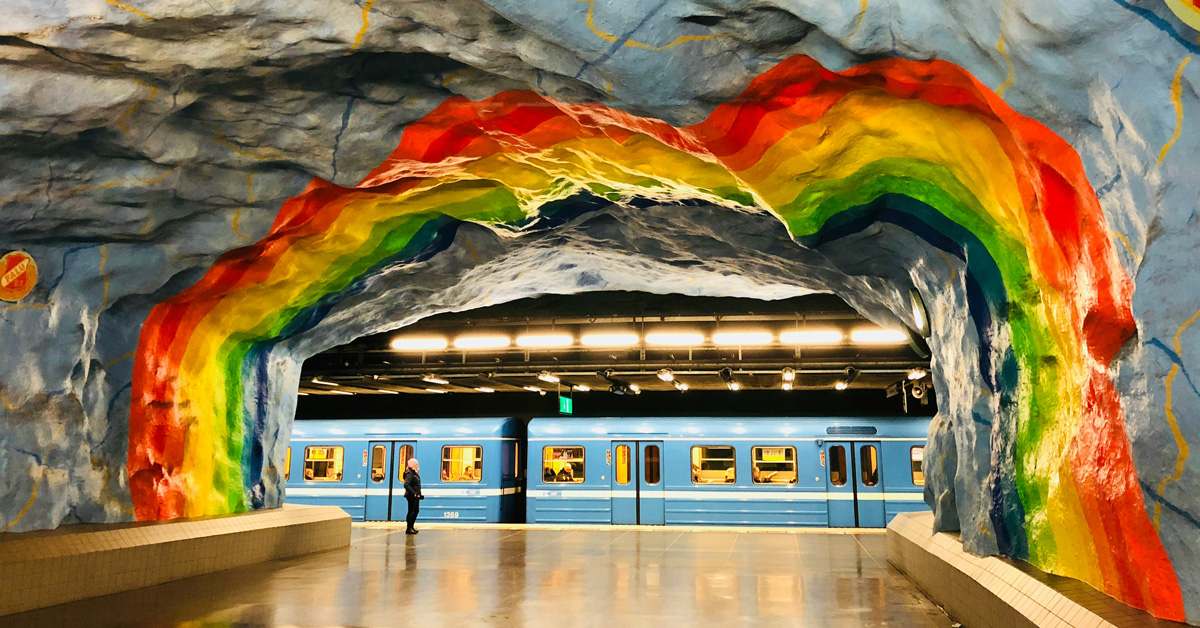
In the past, hard lessons have been learned in various tunnel fire accidents. A major turning point was the London metro fire in 1987. After this incident, tunnel designers have paid much more attention to fire safety. Indeed, a huge leap in positive progress has been made.
Tunnel dampers can be divided into two groups (that may overlap to some extent). Their structure is similar: steel blades are attached to a rectangular frame, opening and closing with actuators. Both damper types are installed in ventilation ducts.
- Fire dampers automatically close in the event of a fire, sealing off the duct. This prevents the flames from spreading through the ductwork and protects the occupants and emergency responders.
- Smoke dampers control the spreading of smoke and hazardous gases. They can be used to isolate the area affected by smoke. Sometimes, by contrast, dampers are opened in specially designed ventilation shafts so that the ventilation system can extract the smoke away from the incident area.
By becoming a 100 percent shareholder in the damper manufacturer Flamgard Calidair in 2023, Halton took a strong foothold in the underground fire safety business.
“Our competitive edge lies in the thoroughly tested, tailor-made equipment that are often designed together with the customer,” says Lee Bramald, Business Development Executive at Halton.
Burning needs
The dampers are tested in large furnaces with temperatures of 400–1000 degrees Celsius and air pressure of up to 6000 pascals or more. This ensures reliability in real-life situations. A typical test can include, for example, opening and closing the steel blades every 10 minutes for two hours using the specialized actuators.
“One particularly demanding client wanted us to test a damper for 100,000 cycles. This is five times more than normally. We managed to do that. After tweaking the product further, we took it to a full million cycles. I got the impression we did convince the customer!”, says Lee Bramald.
Intensive, months-long testing periods guarantee that the actuators, bearings, seals, and other critical parts are reliable in any circumstances. Testing also ensures that dampers comply with international fire safety standards such as BS 476 and UL 555.
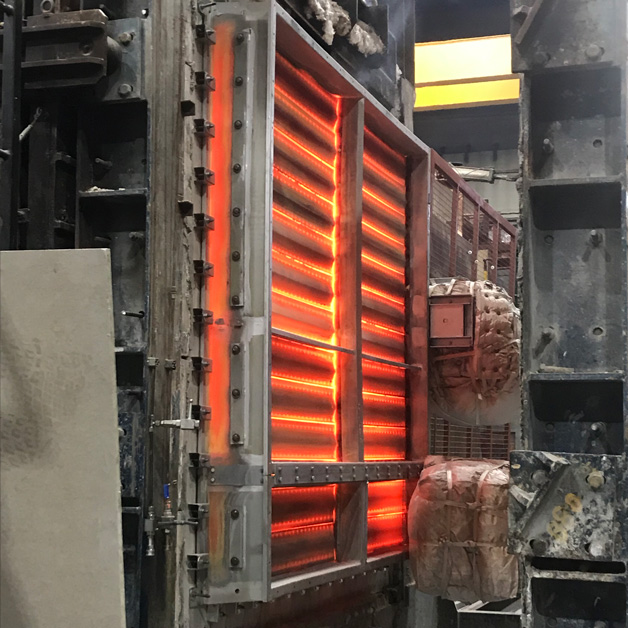
Power optimization by design
Ventilation technology is always inherently tied to energy efficiency, and tunnel dampers are no exception. When the parts of the damper allow the air to flow as smoothly as possible, less electricity is needed in the fans, and they can be smaller in size. This kind of energy optimization can make a big difference during the lifespan of the ventilation system.
Every tunnel project is unique, and ventilation equipment need to fit the desired airflow requirements smoothly. One size does not fit all. To meet the flexibility needs, the Halton-Flamgard dampers are manufactured by one-millimeter increments which ensures desirable fit for any layout. Actuators can also be positioned in a bespoke manner, adding further adaptability.
“When it comes to cost, we have an ace up our sleeve. Halton has factories around the world. This means the transportation costs will probably remain reasonable, wherever the customer project may be located on this planet. In a large tunnel project, hundreds of heavy-duty dampers are needed. If the manufacturer is far from the construction site, the transportation can cost a seven-figure sum,” Lee explains.
Halton-Flamgard’s tunnel damper references include:
- Riyadh Metro, Saudi Arabia
- London Metro, UK
- Helsinki Metro, Finland
- Monaco Tunnel, Monaco
- A86 Paris highway tunnel, France
- Sydney Metro, Australia
- Bangkok Metro, Thailand
- Taipei underground railway, Taiwan
- Istanbul Metro, Turkey
More information
Lee Bramald
lee.bramald@halton.com